Today, Lethex is synonymous for Quality Products and Quality People, making us a Quality Brand.
The Detailed Process
- Cell Grading
- Cell Shortening – Resistance Test
- Assembly in Holder
- Spot Welding
- Battery Capacity Test
- Moulding
- Wiring
- Compensive Test
- Thermal Test
- Barcoding
Cell Grading:
Voltage | Amp | Life Cycle
Cell Grading is an essential process in the manufacturing of lithium-ion batteries. It involves the evaluation and classification of cells based on their voltage, amp, and life cycle. The goal of cell grading is to ensure that the batteries that are produced meet the highest standards of quality and performance.
At Lethex, we have a team of experts who are dedicated to the cell grading process. They perform a series of tests on each cell to determine its voltage, amp, and life cycle. Based on the results of these tests, the cells are classified into different grades. Only the cells that meet or exceed the industry standards are used in the manufacturing of our batteries.
The voltage of a lithium-ion battery is an important factor in determining its performance. The cells that have a higher voltage are considered to be of higher quality and have a longer life cycle. The amp is also an important factor as it determines the current flow and capacity of the battery. The life cycle of a battery is the number of times it can be charged and discharged before it loses its capacity. Cells with a higher life cycle are considered to be of higher quality.
In addition to cell grading, Lethex also invests in research and development to improve the performance of our batteries. We work closely with our global business partners and stay up-to-date with the latest technology in the field of energy storage batteries. This allows us to manufacture batteries that are not only of high quality but also efficient and cost-effective for our customers.
By constantly emphasizing innovation, extensive geographic footprint and strong relationship with marquee clients and steady technology upgrades with global business partners, Lethex has emerged as a distinct frontrunner in the energy storage batteries space for automotive and other diverse applications.
Overall, cell grading is a crucial step in the manufacturing process at Lethex. It ensures that our customers receive high-quality batteries that meet or exceed industry standards. Our commitment to cell grading, along with our focus on innovation, makes us one of India’s most reliable and trusted brands in the lithium-ion battery industry.


Cell Sorting – Resistance Test
Cell Sorting – The resistance Test is a process of evaluating and classifying lithium-ion batteries based on their internal resistance. It is an important step in ensuring that the batteries produced meet the highest standards of quality and performance. The test is performed by measuring the resistance of each cell using specialized equipment. Cells with higher resistance are considered to be of lower quality and are rejected. This process helps to identify and eliminate cells with poor performance, which can be caused by manufacturing defects, damage or ageing. The result of the resistance test is used to sort the cells into different grades, ensuring that only the highest quality cells are used in the final product. Cell sorting – Resistance Test is a crucial step in the manufacturing process of lithium-ion batteries, and it helps to ensure that the batteries produced are safe, efficient, and reliable.
Assembly in holder
Assembly in a holder is a process used to assemble and connect multiple lithium-ion battery cells into a single unit. It is an important step in the manufacturing of batteries for various applications. The assembly process involves placing the cells into a holder, also known as a battery pack, and connecting them in series or parallel. The holder is designed to protect the cells from external damage and to provide a consistent and stable environment for the cells to operate in.
The process of assembling the cells in a holder can be done manually or with the help of automated equipment. The manual process is typically done in small-scale production and requires a high level of skill and precision. Automated equipment is used in large-scale production and allows for faster and more consistent assembly. The equipment is programmed to ensure that the cells are placed in the holder with the correct orientation and that the connections are made properly.
The choice of the holder depends on the final application of the battery. The holder should be able to withstand the environment in which the battery will be used. For example, a holder used in an automotive application must be able to withstand high temperatures, vibration and impact.In summary, Assembly in a holder is an important step in the manufacturing of lithium-ion batteries. It involves placing the cells into a holder and connecting them in series or parallel. The process can be done manually or with automated equipment and the holder should be able to withstand the environment in which the battery will be used. It helps to protect the cells and provides a consistent and stable environment for the cells to operate in.


Spot Welding
Spot welding is a process that uses heat generated by an electric current to create a weld between two metal surfaces. It is a common method used to connect battery cells in lithium-ion batteries. The process involves passing an electric current through two electrodes, which are then pressed against the metal surfaces to be welded. The heat generated by the current melts the metal at the point of contact, creating a weld.
Spot welding is a fast and efficient method that allows for the production of high-quality welds with minimal heat distortion and deformation. It is a commonly used method in the production of lithium-ion batteries as it allows for the efficient and reliable connection of multiple cells. The process is automated, to ensure consistency and precision in the welding process. Spot welding is also cost-effective, as it requires minimal preparation, and the equipment is relatively inexpensive.
Overall, spot welding is a critical step in the manufacturing of lithium-ion batteries. It is a fast, efficient and reliable method of connecting cells, which ensures the consistency and precision of the final product.
Battery Capacity Test
A battery Capacity Test is a process used to evaluate the performance and capacity of a lithium-ion battery. It is an important step in ensuring that the batteries produced meet the highest standards of quality and performance. The test is performed by charging the battery to its full capacity and then measuring the amount of energy that can be discharged from the battery over a specific time. The test is typically performed at different levels of discharge (such as 50%, 75%, and 100%), and the results are recorded.
The capacity test helps to determine the overall health and performance of the battery. It helps to identify any issues such as manufacturing defects, damage or ageing that can affect the battery’s capacity. The results of the capacity test are used to sort the batteries into different grades, ensuring that only the highest quality batteries are used in the final product.
It is also used to compare the capacity of different batteries, and to determine the most efficient and cost-effective option for a specific application. The capacity test can be performed manually or with automated equipment and the results are typically reported in Ampere-hours (Ah). Battery Capacity Test is a crucial step in the manufacturing process of lithium-ion batteries, and it helps to ensure that the batteries produced are safe, efficient, and reliable.


Moulding
Moulding is a manufacturing process that involves shaping a material, such as plastic or metal, into a specific shape or form using a mould. It is a common method used to create complex and precise shapes in lithium-ion battery production. The process typically involves heating the material to a specific temperature and then shaping it by pressing it into a mould.
There are several types of moulding methods, including injection moulding, compression moulding, and vacuum forming. Injection moulding is a widely used method in lithium-ion battery production, where it is used to create housing for the battery cells. This method involves injecting the plastic material into a mould under high pressure, which allows for the creation of precise and complex shapes.
Moulding allows for the efficient and precise production of complex and intricate shapes, which is essential in the manufacturing of lithium-ion batteries. It also allows for the use of various materials, including plastic and metal, which makes it a versatile process that can be adapted to different applications. Moulding is a critical step in the manufacturing of lithium-ion batteries, and it helps to ensure that the final product is safe, efficient, and reliable.
Wiring
Wiring is the process of connecting electrical components to create a functional circuit. It is a critical step in the manufacturing of lithium-ion batteries. The process involves connecting the battery cells, the control circuit and other electronic components together using electrical wire. The wiring process is done to ensure that the battery cells are connected in the correct orientation and that the connections are made securely and reliably.
The wiring process can be done manually or with the help of automated equipment. Automated equipment ensures that the connections are made quickly, efficiently, and with minimal errors. The wiring is also done keeping in mind the safety and protection of the battery cells and other components. The process is critical to ensure that the final product is safe, efficient, and reliable.
Overall, wiring is a crucial step in the manufacturing of lithium-ion batteries. It is a process of connecting the battery cells, control circuit and other electronic components to create a functional circuit. The process is done to ensure that the final product is safe, efficient, and reliable.


Comprehensive Test
Comprehensive testing is the final step in the manufacturing of lithium-ion batteries. It is a process of evaluating the performance, safety, and reliability of the battery as a whole. The test involves a series of individual tests, such as capacity tests, voltage tests, and safety tests, which are conducted to ensure that the battery meets industry standards and customer specifications.
The comprehensive test helps to identify any issues with the battery such as manufacturing defects, damage or ageing that can affect the battery’s performance and safety. The results of the test are used to sort the batteries into different grades, ensuring that only the highest quality batteries are used in the final product.
The comprehensive test can be done manually or with automated equipment. The test is designed to simulate different usage conditions, such as high and low temperature, overcharge and over-discharge, and extreme vibration, to ensure that the battery can withstand different environments.
Overall, comprehensive testing is a critical step in the manufacturing of lithium-ion batteries. It is a process of evaluating the performance, safety, and reliability of the battery as a whole, and it helps to ensure that the final product is safe, efficient, and reliable.
Thermal Test
Thermal testing is a process used to evaluate the performance of a lithium-ion battery under different temperature conditions. It is an important step in ensuring that the batteries produced meet the highest standards of quality and performance. The test is performed by exposing the battery to different temperature conditions and then measuring its performance, such as capacity, voltage, and internal resistance.
The thermal test helps to identify any issues with the battery such as manufacturing defects, damage or ageing that can affect the battery’s performance and safety under different temperature conditions. It also helps to determine the optimal operating temperature range for the battery, which is crucial in ensuring its safety and performance in the intended application.
The thermal test can be done manually or with automated equipment. It is typically performed at different temperatures such as low, normal and high temperatures, to simulate different usage conditions.
Overall, thermal testing is a critical step in the manufacturing of lithium-ion batteries. It is a process of evaluating the performance of the battery under different temperature conditions, and it helps to ensure that the final product is safe, efficient, and reliable in different environments.

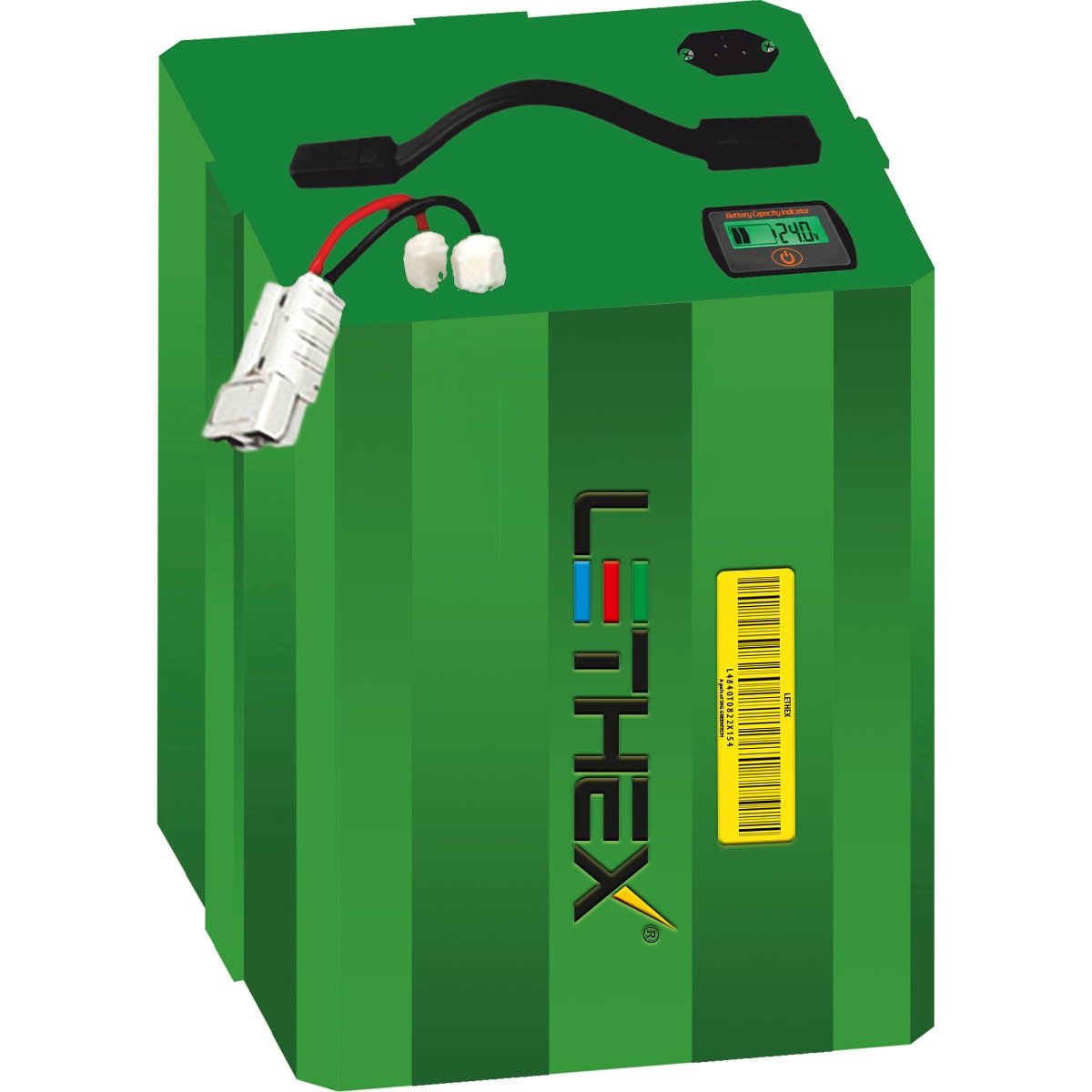
Barcoding (Date of Mfg.)
Barcoding is the process of encoding information, such as the date of manufacturing and other details, onto a barcode label. This process is used in the manufacturing of lithium-ion batteries to ensure traceability and to provide important information about the battery. This information can include the date of manufacturing, batch number, and other important details.
The barcode label is typically placed on the exterior of the battery or the battery pack. This information is then scanned and recorded, allowing for easy identification and tracking of the battery throughout the manufacturing process and distribution chain. This allows for easy identification of the battery in case of any issues and traceability of the battery in case of any recall.
Bar-coding is an efficient and cost-effective way of collecting data, as it eliminates the need for manual data entry, and allows for quick and accurate data collection. This information can also be used for quality control, inventory management, and compliance with regulatory requirements.
Overall, barcoding is an important step in the manufacturing of lithium-ion batteries. It allows for traceability and provides important information about the battery, such as the date of manufacturing and other details. This information can be used for quality control, inventory management, and compliance with regulatory requirements.


